導入事例
「見える化」この”稼働管理システム”は他に無い柔軟性を持つ。工場内の『5つ 』のポイントを改善!
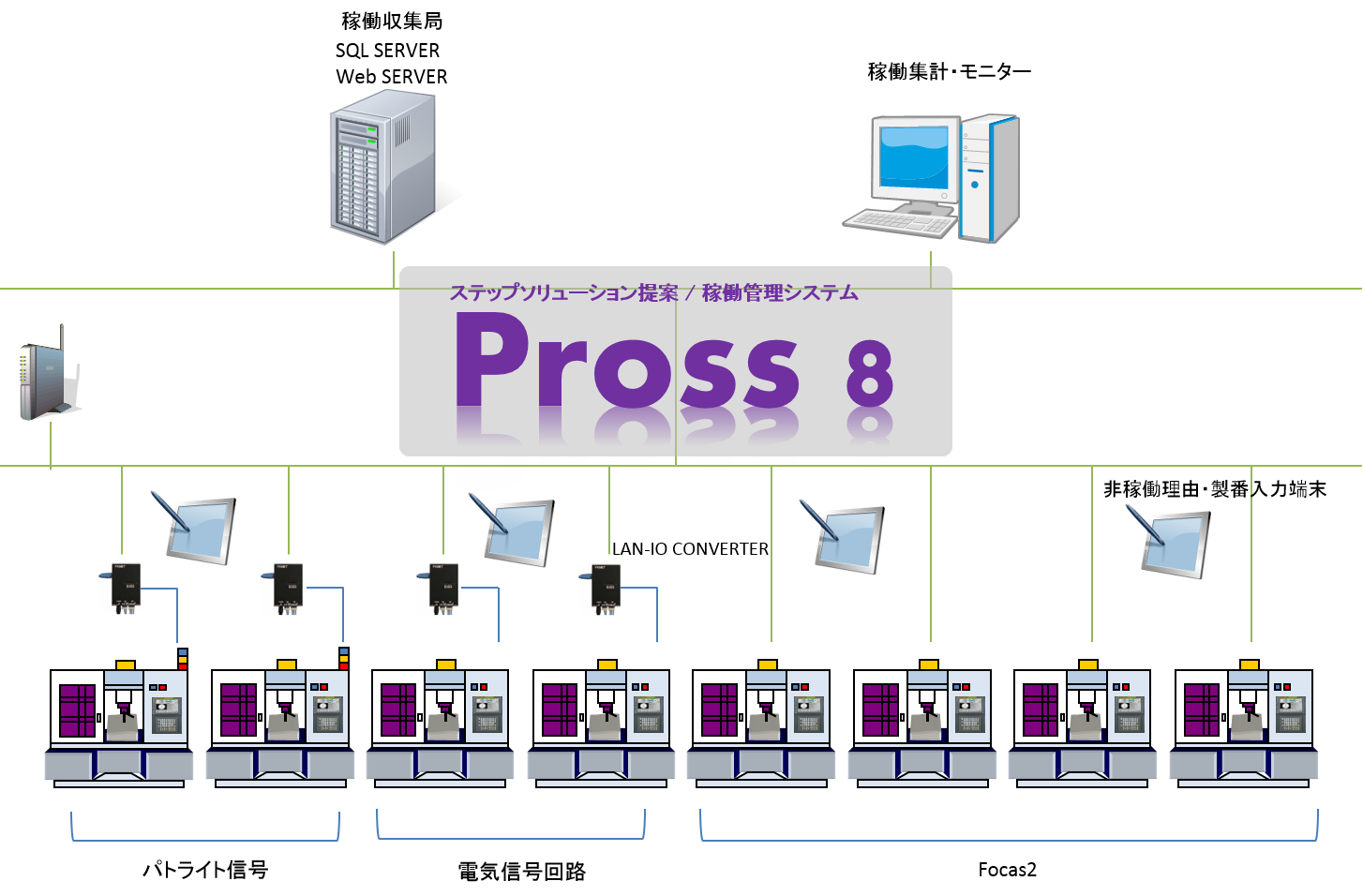
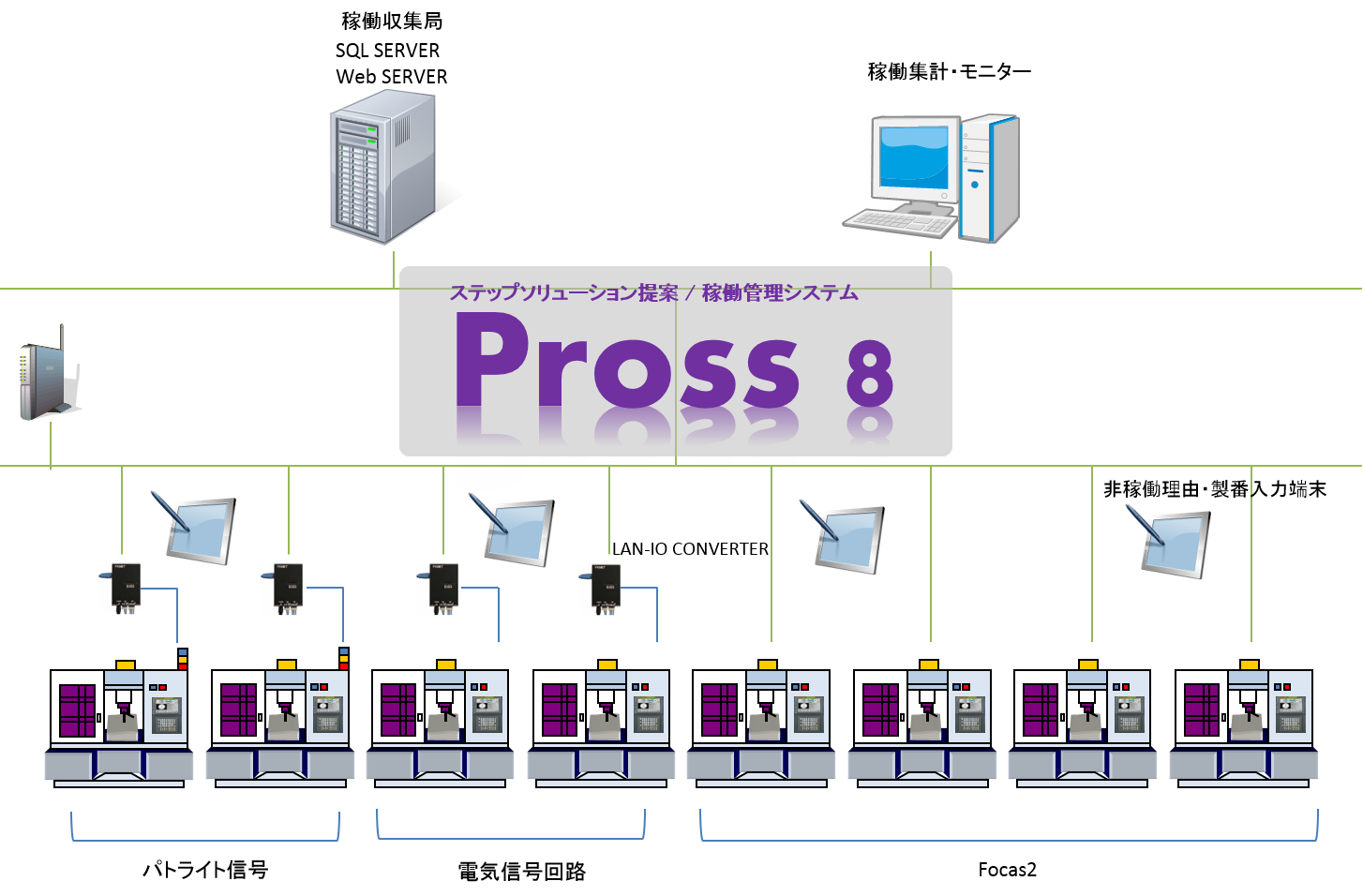
- ソフトウェア
- 生産性向上
- 自動化
- 環境改善
-
課題
【①手動管理】仕事増でヌケモレ
【②予測不足】終わってみたら「赤字」
【③活用不足】機械稼働読めず
【④専任問題】属人化した管理業務
【⑤工数問題】手作業他、工数かかる
-
解決策
要件に柔軟対応できるPross8で解決
貴社に合ったPross8 の開発
1つずつステップアップ開発
”課題を克服する貴社のシステム” 完成
-
成果
【①管理改善】要所を管理
【②予測対策】予測強化で無駄の潰しこみ
【③リソース活用】データ活用で無駄稼働10%減
【④標準化】簡単操作、誰でも管理
【⑤工数削減】報告書の作成工数削減
課題の背景
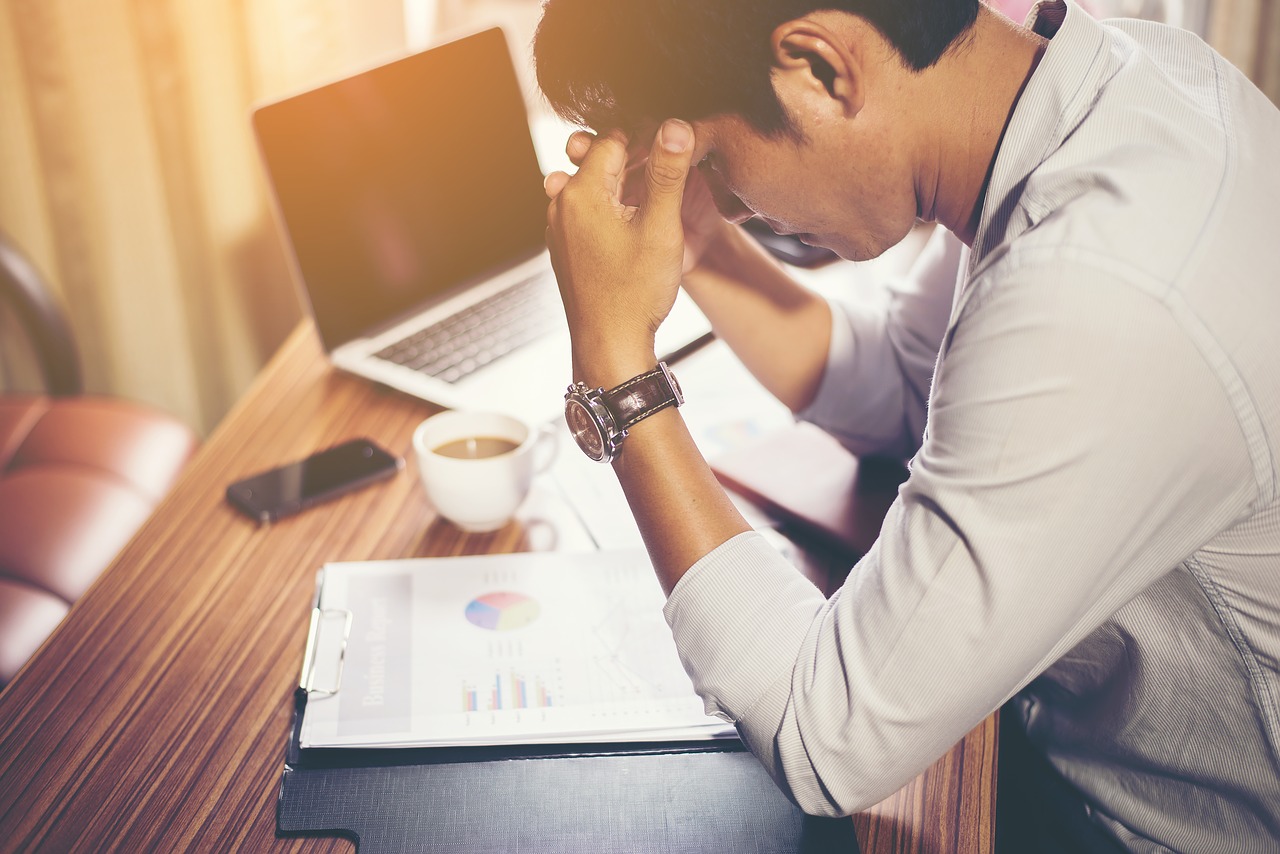
製造現場で、人による機械稼働管理が限界に達した。管理方法を見直し、生産性向上を実現したい
<解決したい課題>
●高齢化による人材不足と旧来の管理方法の限界
●将来的な事業拡大を見据えた工場内の可視化と適切な設備管理
●カスタマイズ性、予防保全、効率化への強い要望
●人的リソースと設備リソースの可視化と活用
●稼働管理体制の整備による生産性・業務・売上向上
自動車部品製造メーカーC社では、製造部門にて生産性向上と効率化を目指し、工程管理の強化を検討されていました。
背景として、高齢化問題。加工現場およびシフト管理の指揮を執る部門長も高齢化。また、新たな仕事の獲得、品質維持のための各種チェック工程なども増え、ベテラン陣の経験や能力頼りの旧来の管理が限界に達していました。
将来的な現場運用・事業拡大も視野に入れ、工場内の機械稼働をより見える化する、設備管理を適切にでき具体的に成果をだす改善をご検討されている際、米沢工機へご相談いただきました。
C社からは、あわせていくつかのご要望がありました。
管理システム導入にあたって、カスタマイズできる点も重視。仕様がガチガチに決まっていて、柔軟な変更のできないシステムでは、社内標準化・浸透させることに難ありという点が1つの壁でした。
他ご要望は、予防保全と効率化についてでした。
過去の請負案件の中には、終わってみたら結果「赤字」の仕事があり大きな問題になったことがありました。当時は、機械の停止をリアルタイムに把握できず、問題発生時に迅速な対応もできませんでした。くわえて、案件完了後に、機械加工時間、機械アイドル時間、他の機械の空き時間など、振り返りのための定量的な数値情報も最終的には抽出できませんでした。定量的な精査ができず具体的な改善へ活かすこともしっかりできなかった苦い経験も踏まえて、今後はそれらも改善して防止保全していきたいという要望も盛り込まれていました。また削減したいものの中で現場から強く要望がったのは日報報告書、元々はすべて手書きで行っており、工数かかる上に稀に記入漏れも発生。定量的に改善に活かされる面でも弱く、改善・削減の要望がありました。
諸々の問題点・要望を踏まえまして、人的リソース・設備リソースの現在状況を適切に行い、仕様の調整も柔軟にできるシステムを検討。
稼働管理体制を整え、生産性カイゼン、業務カイゼン、売上向上へ繋げていく。
選んだ理由
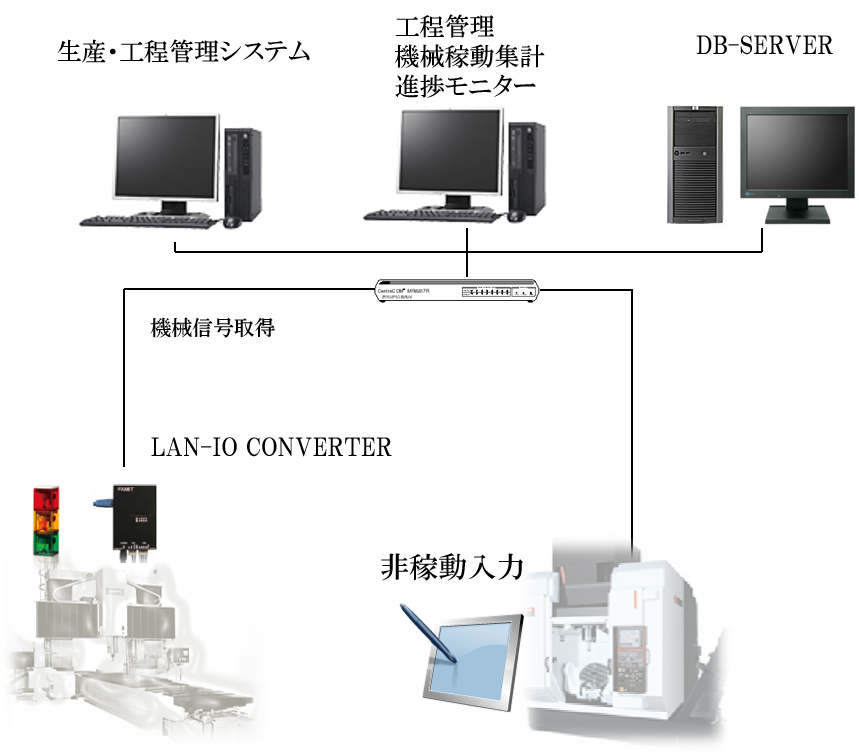
複数メーカー製品の混在する現場。米沢工機とファットシステムによるご対応。
■製造年式やメーカーが異なる工作機械に接続可能な製品
現場には、年式やメーカーなど仕様や規格が違う様々な工作機械が混在。稼働信号を取得したい全ての工作機械から稼働信号を取得するのは困難。ファットシステムの「稼働管理システム」では、メーカーや製造年月の違う多種多様な工作機械であっても、仕様に合わせた方法で稼働信号を取得可能。
■カスタマイズ性
カスタマイズ対応に特にすぐれている同社製品をご提案。
■YONEZAWAのものづくりサポート
設備環境、現課題解決を分析いただき、システムの中でも適切なものをピックアップして提案。設備メーカー、周辺機器メーカー、フォットシステム、各社をとりまとめ、稼働管理システム導入からその後のサポート体制まで提供。
解決策の背景
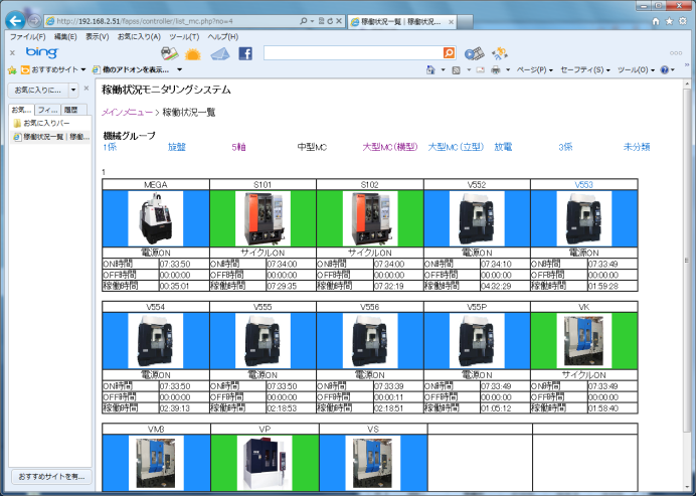
ファットシステムの「稼働管理システム」、
段階を踏んだステップ毎の導入によりC社の要求に合わせたシステム構築を実現
キーポイント1)段階を踏んだステップ毎の導入提案
課題の大半は「 加工現場の IoT 」と「客先に会ったアプリケーション開発」とで解決可能です。但し、全てのシステムを一度に立ち上げるとコストも高く、問題点も把握し難い為、段階を踏んでのステップアップをご提案しております。
キーポイント2)段階毎に、最適な姿を十分な議論を基に実現
ステップ毎に、「あるべき姿」を議論しながら、構築を進めます。
お客さま自身では気づけないこと、パートナー企業だけでは想定できない部分を米沢工機からフォロー。
お客さまへ伴走しプロジェクトを推進いたします。
キーポイント3)お客さまごとの要求に合わせたシステム構築を実現
ステップ1『 加工現場の加工機データ』、ステップ2『人の役割の変化』、ステップ3『新たなデータ活用へのアプリケーション開発と添加』と、ステップアップしながら、段階的に積上げ製作。
カスタマイズ対応可能なシステムにより、最終的に、お客さまの要求に合わせて課題を克服するシステム構築を実現します。
成果の背景

製造現場の「見える化」で実現された現場改善
【①効率稼働】【②予測対策】【③リソース活用】
⇒管理システム導入直後と比較して、機械の有効稼働時間10%削減。
設備毎の稼働率を分析することでボトルネックとなっていた工程、設備を特定しカイゼン。新規設備なのに「メンテンス頻度が高い」、古い設備であっても「稼働率が高い」など、設備ごとの稼働状況も定量評価できるよう見える化。分析し、見込みの数値の精度も向上、ムリムダを抑えた効率的な生産計画へ繫がりました。工場全体での機械稼働効率、人と機械の生産性もカイゼンされました。
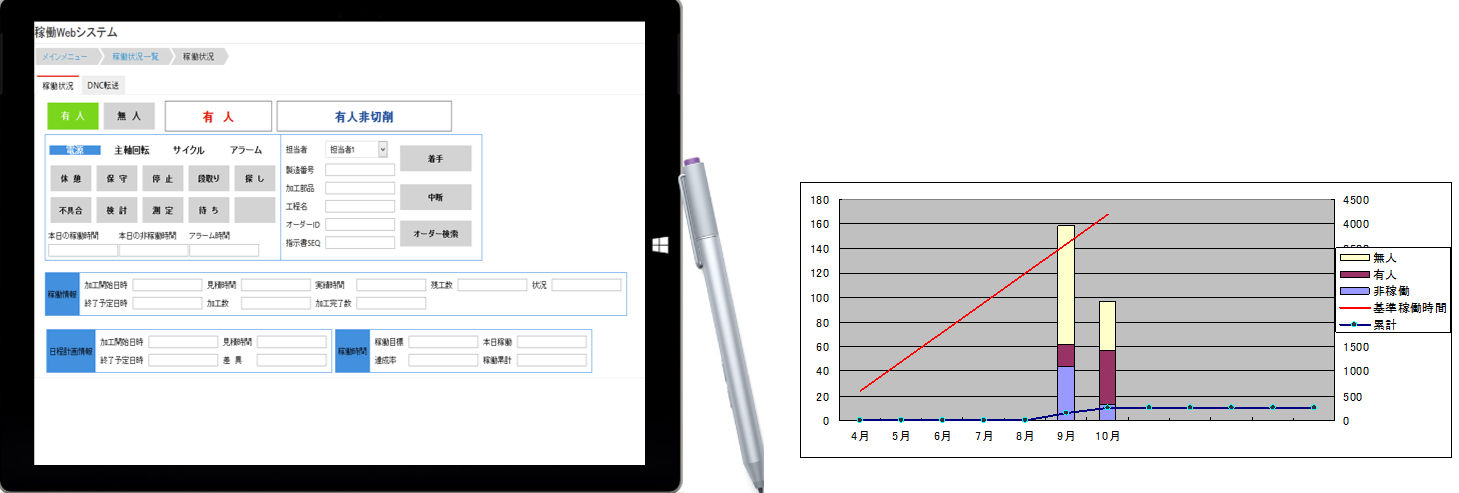
【④標準化】【⑤工数削減】
⇒簡単な操作で誰でも扱えるシステム。報告書の作成工数も削減し、品質も向上。
システムの機能についても、少し操作を憶えれば、誰でも管理が可能。部署内における作業の標準化を実現。
報告書の作成工数削減とペーパーレス化実現。報告書の品質向上につながり、また、過去の稼働実績を素早く検索できるのが非常に効率的で便利。
【更に】
稼働管理システムによる改善を進めながら、米沢工機からは「お客さまとやりとりした情報をもとに、工場内フローやボトルネック箇所の改善」のご提案。搬送、ルーティーン作業を補助する周辺設備等。作業効率向上につながる改善提案をし実現。
今後YONEZAWAへ期待する事
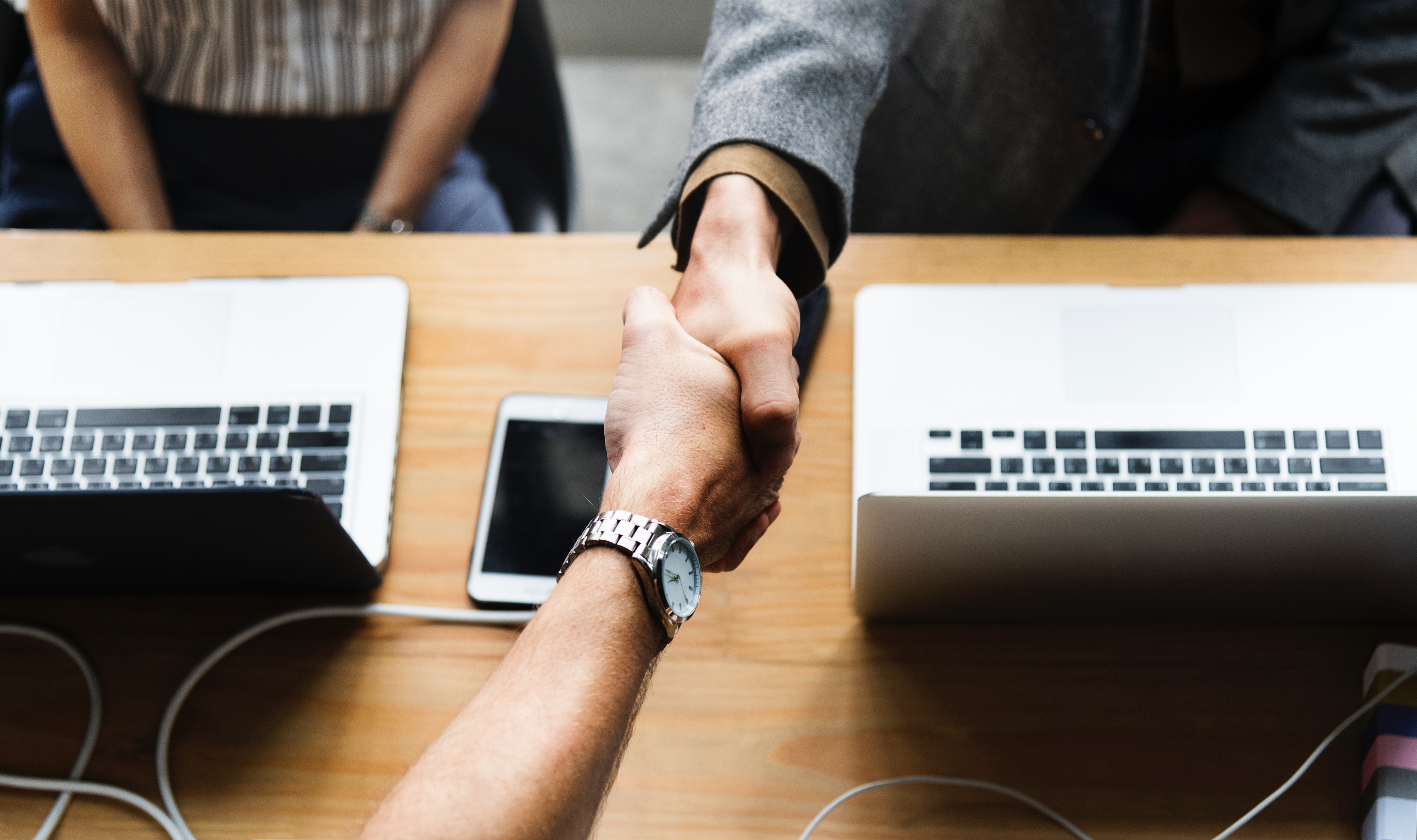
カイゼンが実感できています。次ステップの稼働管理システム導入支援とあわせて、今後も引き続き生産設備提案と、運用面でのフォローとサポートを期待。
<米沢工機 :担当後記>
YONEZAWAは、パートナー企業さまとともに大手自動車メーカーさま工場インフラ改善提案から少数精鋭の専門企業さままで、グローバルに各々の生産課題解決の為の自動化ソリューションを創出し、ご提案してまいりました。
私たちは、ファクトリー・オートメーション・テクノロジー(Factory Automation Technology)の実現を目指し、また自動車業界におけるCASE化(Connected、Autonomous、Shared、Electric)の取り組みにも挑戦し続けます。稼働管理システム含め、工程管理システム、、機上計測システム、DNCシステムなどテクノロジー、IoT情報の集計技術等もご相談ください。IoTの進化を柔軟に取り入れ、現場実務に適した製品をご提案いたします。